How Thermocouples and RTD Pt100 Sensors Are Used in Plastic Extrusion Machinery
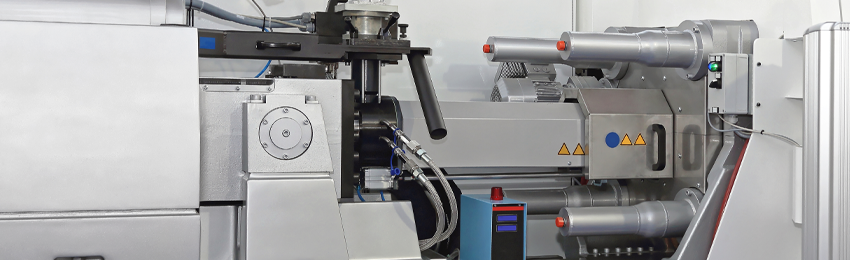
Contents
Introduction
Plastic extrusion is a critical process in manufacturing plastic products, from pipes and sheets to films and complex profiles. Temperature control is fundamental to ensuring product quality, consistency, and process efficiency. Thermocouples and RTD Pt100 sensors play an essential role in monitoring and regulating temperature throughout the extrusion process. This article explores their functions, placement, and benefits in plastic extrusion machinery.
The Importance of Temperature Control in Plastic Extrusion
Plastic extrusion involves heating raw polymer material, melting it, and forcing it through a die to create a continuous shape. Maintaining precise temperature at different stages of the process ensures:
- Consistent material flow
- Proper melting and homogenization
- Minimization of defects (such as warping or uneven thickness)
- Energy efficiency and machine longevity
Both thermocouples and RTD Pt100 sensors are widely used in extrusion machinery to measure and control temperatures across different zones.
Where Thermocouples and RTD Sensors Are Used in Extrusion Machinery
Temperature sensors are strategically placed at key points in the extrusion process:
- Barrel Heating Zones: The extruder barrel is divided into multiple heating zones, each requiring precise temperature control to progressively melt the plastic. Thermocouples (typically Type J or K) are often embedded in the barrel wall to provide real-time temperature feedback to the control system. For higher accuracy and stability, RTD Pt100 sensors are sometimes used, particularly in applications where long-term consistency and precision are crucial.
- Screw Temperature Monitoring The rotating screw inside the barrel helps mix and move the molten plastic forward. In some advanced extrusion systems, sensors are placed near or on the screw to monitor its temperature and ensure optimal processing conditions.
- Die Temperature Control: The die at the end of the extruder shapes the molten polymer into the desired profile. Temperature fluctuations at this stage can cause defects such as inconsistent thickness or surface imperfections. Thermocouples or RTDs are placed in the die assembly to maintain the correct temperature.
- Melt Temperature Sensors To ensure uniform melting, thermocouples are placed in direct contact with the molten plastic before it exits the extruder. These sensors help maintain the correct viscosity, preventing underheating or overheating, which can affect product strength and appearance.
- Cooling Zones and Calibrators After extrusion, the plastic must be cooled at a controlled rate to prevent warping. RTD Pt100 sensors, known for their precision in lower temperature ranges, are commonly used to monitor cooling water or air temperatures.
Choosing Between Thermocouples and RTDs in Plastic Extrusion
Both thermocouples and RTD Pt100 sensors have their advantages:
Thermocouples
Thermocouples (e.g., Type J, K) are preferred for high-temperature regions due to their fast response time and durability in extreme heat.
RTD Pt100 Sensors
RTD Pt100 sensors provide superior accuracy and stability, making them ideal for applications requiring precise temperature measurement over long periods.
Many extrusion machines use a combination of both sensor types, depending on the zone's specific temperature requirements.
Conclusion
Thermocouples and RTD Pt100 sensors are indispensable in plastic extrusion machinery, ensuring accurate temperature control across various process stages. By strategically placing these sensors in barrel zones, screws, dies, and cooling areas, manufacturers can maintain product quality, improve efficiency, and reduce waste. Choosing the right sensor type for each application enhances reliability and optimizes performance in plastic extrusion operations.
Note: These application examples are provided to illustrate potential uses of our products across various industries. However, it is important to note that final product selection should be based on your specific application requirements, standards, and industry regulations. The suitability of any of our products for a particular application is entirely at the discretion of the purchaser as being the best judge for that particular application.
For application-specific advice, please contact us — one of our engineers will be happy to assist with technical guidance.
Further Reading
Learn more about Temperature Controllers
Explore our range of temperature controllers from simple PID cpontrollers to complex programmers.
Explore our range of Thermocouples and RTD Pt100 sensors for plastics machinery applications
Discover the various designs of temperature sensors for the plastics industry.
Looking for temperature Instrumentation?
View our range of temperature instrumentation for use with thermocouples and resistance thermometers.