What is a Pt100 Sensor - Reference Information
What is a Pt100?
A Pt 100 is a type of resistance temperature sensor made using a Platinum element with a resistance of 100 ohms @ 0ºC and typically with a 38.5 ohm fundamental interval (change in resistance over the range 0 to 100ºC). Pt100 Sensors are used for a wide variety of temperature measurement applications. They are also commonly referred to as PRT and RTD Sensors. There are many styles of Pt 100 Sensor in a wide range of designs and constructions. Pt1000 sensors are also available.
Typical Pt100 Sensors
Mineral InsulatedPt100 Sensors
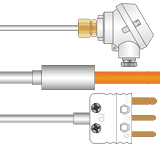
Pt100 Sensors
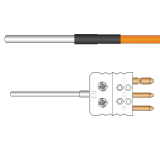
Pt100 Sensors
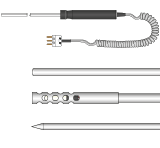
Surface Measurements
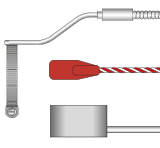
IEC 60751 Standards and Tolerances
For the purposes of the IEC 60751 standard, the RTD itself comprises the sensing resistor within its protective sheath (if applicable), internal connecting wires and external terminals for onward connection. Mounting equipment and connection heads can also be included. IEC 60751 actually applies to industrial devices, primarily sheathed, over the temperature range -200°C to 850°C, and offers two tolerance classes, A and B - these defining the maximum deviation in degrees Celsius from the nominal temperature relationship table figures. Class A RTD’s can show deviation of ±0.06 ohms (±0.15°C) at 0°C, while Class B sensors can be within ±0.12 ohms (±0.3°C) at 0°C.
Standard thermometers are constructed from platinum, having an a coefficient of 3.85 x 10-3/°C. Having nominal resistances of 100 ohms or 10 ohms at 0°C (the latter harnessing heavier gauge wire) and being aimed at use in the range above 600°C. With 100 ohm devices, Class A only applies up to 650°C; also the A classification is not applicable to two wire devices (see Part 3, Section 3). Clearly, devices which conform to the standard as defined can be interchanged - always useful!
The standard also covers a range of other factors - but not construction. For example, the RTD’s have to be suitable for DC and AC current measuring systems - the latter up to 500Hz. So there are certain inductance and coupling constraints on design. Insulation resistance, response times, self-heating effects, immersion errors, thermo-electric effects, tests for temperature limits and temperature cycling, mechanical vibration and pressure effects are also specified.
IEC 60751 also says that manufacturers can reveal electrical characteristics, like thermometer capacitance, capacitance to earth, and inductance, as well as the ohmic resistance of the internal connecting wires. Also, calibration immersion depth, minimum usable depth, thermal response time and self-heating effects can be stated.
Basic Sheathed RTD Assemblies
Lower cost general purpose industrial platinum RTD sensor assemblies, typically covering the temperature range -100°C to +350°C (although this can be customised), embody, as standard, detector elements with a resistance of 100 ohms at 0°C as per IEC 60751 Class B, although alternative element resistances and tolerances are available. Class A elements, for example, can normally be provided, offering down to ±0.01% accuracy, if required. The sensors themselves normally consist of environmentally resistant pure, doped strain-free platinum wire-wound elements encased in either a high temperature, expansion matched glass or a high purity ceramic envelope, although a thick or thin film RTD element can also be used.
These assemblies are available with single, duplex and triplex sensor element assemblies all normally offering two, three and four wire connection lead configurations as standard (the four wire versions will be available for connection in compensated or blind loop format - for bridge and potentiometric measuring circuits). Attachment lead-out wires are generally fabricated from Kapton-insulated (or similar) copper.
Typically, minimum immersion depth of these devices will be approximately 50mm. The recommended measuring current will be less than 5mA and insulation resistance between the leads and sheath at 240V will be better than 100 Mohms at ambient temperature.
Sheath tips can be designed to suit the application, there normally being a range of constructions, including those with reduced tips and thin sheath walls. Pierced shroud versions are also available for air and gas temperature measurement. Voids within the sheath are normally packed with inert material, for optimum heat transfer characteristics, and the sheaths are hermetically sealed to provide protection against moisture, corrosion and vibration.
Sheaths are generally available with diameters from 0.5mm to 13mm as standard in virtually any sensible length, with bends to suit the application. Materials start with 316 stainless steel, although other grades of steel, Inconel 600, Incoloy 800, nickel, nickel alloys and other materials are usually available. Further, many manufacturers will also provide a range of fluoroplastic sheath cladding materials for the more demanding and corrosive environments.
End seals will be available in a range of shapes, sizes and materials. As standard, most manufacturers’ basic platinum RTD ranges offer end seals covering the full spectrum of user requirements, from basic laboratory termination heads, connector blocks and quick release plugs, through hand-held devices, and on to full industrial, heavy duty enclosures complete with ruggedised protection tubes, thermowells and head-mounting connectors or transmitters.
Mineral Insulated Metal Sheathed RTD Assemblies
As with commercially available thermocouples, a popular style of RTD assembly is the mineral insulated metal sheathed (MI or MIMS) version. Basically, it is very similar to its thermocouple counterpart, comprising a metal, seamless, semi-flexible, high integrity, hermetically sealed probe enclosing the same compacted mineral insulant powder (usually, magnesium oxide) which supports and insulates the RTD element and lead wires.
The devices are compact, self-armoured, yet flexible. As with thermocouples, there are many advantages. These include small size, ease of installation (they can be bent, twisted and flattened without problems), good mechanical strength, excellent insulation resistance (100Mohm between sheath and conductors), good long term accuracy and stability and acceptably fast response rates. They can cope with most industrial environments, including the extremes, like those with high vibration and high pressure or vacuum, as well as corrosive and aggressive media.
Temperature ranges covered are typically from -100°C to +600ºC, typically using 100 ohm resistance at 0°C IEC 60751 Class B RTD platinum sensor assemblies in single or duplex element configurations. As with other sheathed assemblies, the sensor elements are normally platinum wire in expansion matched glass or high purity ceramic, with film sensor versions optionally available. More sophisticated, high precision Class A , 1/3, 1/5 & 1/10 DIN elements (see Part 1, Section 4) can also be provided, giving greater accuracy.
Again, as with most other sheathed RTD assemblies, two, three and four wire configurations are almost always supported. Lead-out wires are typically insulated copper. Recommended energising current limit will be 5mA. Minimum immersion depth for the probes is typically 50mm.
Sheath wall thickness is normally about 15% of the overall probe diameter, and this construction resists creasing and splitting well, typically allowing bending with radius about 12 times the OD (although this can be reduced to 4 x with the use of a mandrel). Sheaths are available as standard normally with 3, 6 and 8mm diameters, and with lengths to suit virtually any requirements. A wide range of sheath materials is typically available, including stainless steel and Inconel 600.
Sheaths can also be bonded with a variety of fluoroplastic coatings for the more corrosive environments. 316 stainless steel gives good corrosion resistance. Inconel 600 sheaths are aimed at applications which are extremely corrosive, also covering carburising atmospheres - but not sulphur bearing atmospheres at the upper temperature limit.
Seal termination styles and sheath fittings usually include most of the wide range described elsewhere on this site, suiting diverse application requirements. These probes are also readily available and are reasonably priced.
With this probe design, there can be problems relating to the ingress of water vapour. This can result inRTD poisoning and reduced insulation resistance, and hence instability and premature failure. This really is, completely avoidable, being a matter of quality control in manufacture & specifying at the point of order.
Extension Leads and Connectors - RTD’s
Interconnection cable for RTD assemblies comes in a number of forms, almost all of which are colour coded to the IEC 60751 international standard (Part 1, Section 4). Typically, the cable is provided as three cores of insulated, stranded, silver plated copper, the wires being inter-woven and finished with a braid screen with outer sheathing. Individual, and two, four and six core cabling are also available. There is also a wide range of insulation, braiding and sheathing materials.
A typical basic extension cable of this type would use PVC insulation and sheathing and the screen would be of tinned copper. Temperature rating would be up to about 105°C. There is then PFA core insulation and sheathing, and braiding made from nickel plated copper. These extension cables are suitable for use up to 260°C, or for short periods, 300°C. Finally, fibreglass insulated and varnished types with stainless steel braiding, these are rated to 480°C.
Clearly, extension cables are not quite as important as they are in thermocouple thermometry. The main consideration is getting the low level signals from point to point with minimum losses and interference from external currents and contactor operation. However, it is important to remember that thermoelectric effects, from the use of different conductors (as per thermocouples), can cause problems, particularly where potentiometric measurement is concerned.
Connectors for RTD’s come into much the same category. The emphasis is on making good, high integrity connections which do not introduce ohmic resistance. High quality RTD connectors should always be used - and these are exactly the same as those used in thermocouple thermometry.