How Thermocouples are used for Gas Turbine Exhaust Monitoring in Power Generation
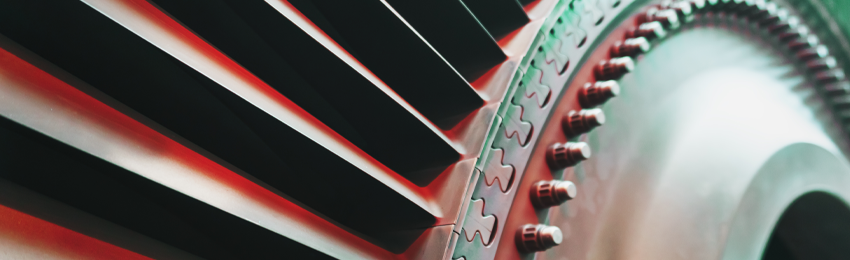
Contents
- Introduction
- The Importance of Exhaust Gas Temperature Monitoring
- Why Thermocouples Are Used in Gas Turbine Exhaust Monitoring
- Types of Thermocouples Used in Gas Turbine Exhaust Monitoring
- Placement of Thermocouples in Gas Turbines
- Benefits of Using Thermocouples in Gas Turbine Monitoring
- Conclusion
- Further Reading
Introduction
Gas turbines are a critical component of power generation, providing efficient and reliable energy for industries and electrical grids worldwide. Monitoring exhaust gas temperature (EGT) is essential for optimizing performance, preventing overheating, and ensuring the longevity of turbine components. Thermocouples are the primary sensors used for gas turbine exhaust monitoring due to their durability, high-temperature tolerance, and fast response times.
The Importance of Exhaust Gas Temperature Monitoring
In a gas turbine, air is compressed, mixed with fuel, and ignited to produce high-temperature exhaust gases that drive the turbine blades. Proper monitoring of exhaust gas temperature is essential for:
- Efficiency Optimization – Ensuring fuel combustion is within the ideal temperature range for maximum efficiency
- Component Protection – Preventing damage to turbine blades, combustors, and other high-temperature components
- Early Fault Detection – Identifying irregularities such as flame instability, fuel distribution issues, or compressor inefficiencies
- Regulatory Compliance – Meeting emissions and safety regulations in power plants
Why Thermocouples Are Used in Gas Turbine Exhaust Monitoring
Thermocouples are the preferred choice for monitoring gas turbine exhaust due to several key advantages:
- High-Temperature Tolerance – Capable of measuring temperatures exceeding 1200°C and in some cases up to 1700ºC
- Fast Response Time – Quickly detects changes in exhaust gas temperature, allowing real-time adjustments
- Durability – Withstands extreme conditions, including thermal cycling, vibrations, and corrosive gases
- Multi-Point Monitoring – Thermocouples can be installed at multiple locations to detect variations across different sections of the exhaust
Types of Thermocouples Used in Gas Turbine Exhaust Monitoring
Several thermocouple types are used for gas turbine exhaust applications, depending on temperature range and environmental conditions:
- Type K (Nickel-Chromium/Nickel-Alumel) – Common for high-temperature applications up to 1100°C continuous use
- Type N (Nicrosil/Nisil) – More stable than Type K and resistant to oxidation, making it ideal for harsh environments
- Type R and Type S (Platinum-Rhodium/Platinum) – Highly accurate, used in critical monitoring points where precision is essential up to 1600ºC continuous and short term up to 1700ºC
Placement of Thermocouples in Gas Turbines
To obtain comprehensive exhaust gas temperature data, thermocouples are strategically placed in key locations:
- Exhaust Gas Temperature Sensors – Positioned at multiple points in the turbine exhaust to monitor temperature distribution
- Combustion Chamber Monitoring – Detects temperature variations within the combustion process
- Turbine Blade Path Sensors – Ensures that blades operate within the correct temperature range to prevent thermal stress
- Stack Exit Monitoring – Measures final exhaust gas temperature to assess overall efficiency and compliance with emissions regulations
Benefits of Using Thermocouples in Gas Turbine Monitoring
Benefits of Using Thermocouples in Gas Turbine Monitoring
- Real-Time Performance Optimization – Enables immediate adjustments to fuel mixture and turbine operation
- Extended Equipment Lifespan – Helps prevent overheating and thermal fatigue, reducing maintenance costs
- Improved Safety – Prevents catastrophic failures caused by excessive temperatures.
- Data-Driven Maintenance – Allows predictive maintenance strategies based on exhaust temperature trends
Conclusion
Thermocouples play a vital role in gas turbine exhaust monitoring, ensuring efficiency, safety, and regulatory compliance in power generation. Their ability to withstand extreme temperatures, provide rapid feedback, and maintain long-term stability makes them the industry standard for this application. By strategically placing thermocouples within the exhaust system, power plants can optimize turbine performance, reduce downtime, and extend the lifespan of critical components.
Note: These application examples are provided to illustrate potential uses of our products across various industries. However, it is important to note that final product selection should be based on your specific application requirements, standards, and industry regulations. The suitability of any of our products for a particular application is entirely at the discretion of the purchaser as being the best judge for that particular application.
For application-specific advice, please contact us — one of our engineers will be happy to assist with technical guidance.
Further Reading
What are the various thermocouple types?
Discover the unique characteristics and temperature ranges for the most popular thermocouple types.
What are the EMF outputs for thermocouples?
View our EMF output tables for all thermocouple types.
Explore our range of Thermocouple sensors for industrial applications
View the various designs of temperature sensors used in a wide range of industries.