High Accuracy Temperature Controllers
Temperature Controllers
Related Products
Mineral Insulated Thermocoupleswith pot seal
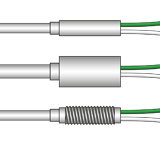
Resistance Thermometers
with pot seal
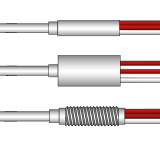
High Accuracy and Resolution
Highly accurate and stable temperature controller which is ideal for high accuracy laboratory experiments as well as applications in tightly controlled environments such as semiconductor manufacturing. The display resolution is 0.001°C with a high accuracy of ±0.05°C.
Bar Graph Display
The front panel bar graph may be programmed to show either the control output status or deviation between the set and process values in 0.1 or 0.01°C increments.
Control
The F9000 features BrilliantTM PID control with autotuning. BrilliantTM PID provides high stability control for both setpoint and process changes.
Fast Input Sampling Time
In order to provide stable control at such a high accuracy, the input signal is sampled at 0.1 seconds (10 times a second). Additionally, it is possible to set integral and derivative terms to 0.1 seconds resolution.
Bias Settings
In addition to the standard process bias function, the F9000 also provides a sensor bias for precise calibration of the RTD sensor to the controller.
Single or Dual Channel
The F9000 is available as a single or dual channel version.
Power Feed Forward
This option constantly monitors the electrical load through a dedicated transformer. The instrument control output is then automatically adjusted to compensate for fluctuations in the power supply.
Highly accurate and stable temperature controller which is ideal for high accuracy laboratory experiments as well as applications in tightly controlled environments such as semiconductor manufacturing. The display resolution is 0.001°C with a high accuracy of ±0.05°C.
Bar Graph Display
The front panel bar graph may be programmed to show either the control output status or deviation between the set and process values in 0.1 or 0.01°C increments.
Control
The F9000 features BrilliantTM PID control with autotuning. BrilliantTM PID provides high stability control for both setpoint and process changes.
Fast Input Sampling Time
In order to provide stable control at such a high accuracy, the input signal is sampled at 0.1 seconds (10 times a second). Additionally, it is possible to set integral and derivative terms to 0.1 seconds resolution.
Bias Settings
In addition to the standard process bias function, the F9000 also provides a sensor bias for precise calibration of the RTD sensor to the controller.
Single or Dual Channel
The F9000 is available as a single or dual channel version.
Power Feed Forward
This option constantly monitors the electrical load through a dedicated transformer. The instrument control output is then automatically adjusted to compensate for fluctuations in the power supply.
Communications
RS485 serial communication (ANSI X3.28) is supplied as standard. This instrument is also compatible with ladder communication protocol for direct connection to a PLC.
Inputs
Due to the high precision of the F9000 only 3 or 4 wire Pt100 platinum resistance thermometers may be used as the instrument input.
Outputs
Solid State Relay Drive output (0-12V DC) or current outputs are available.
Digital Input Contact
A digital contact input is provided for remote selection of control run/stop.
Alarms
Two alarms are provided as standard. Temperature, process, deviation or setvalue alarms may be selected. An instrument ‘fail’ contact is also provided..
Analogue Output
A second analogue output may be specified as a retransmission signal of: process value, set value, deviation or as a control output.
Calibrated Sensor
A UKAS calibrated Pt100 sensor is available for use with the F9000 controller which uses bias features to match the sensor to the controller. Please contact TC Ltd. for details.
Supply
A choice of 85/264V AC or 24V AC/DC supplies is available.
RS485 serial communication (ANSI X3.28) is supplied as standard. This instrument is also compatible with ladder communication protocol for direct connection to a PLC.
Inputs
Due to the high precision of the F9000 only 3 or 4 wire Pt100 platinum resistance thermometers may be used as the instrument input.
Outputs
Solid State Relay Drive output (0-12V DC) or current outputs are available.
Digital Input Contact
A digital contact input is provided for remote selection of control run/stop.
Alarms
Two alarms are provided as standard. Temperature, process, deviation or setvalue alarms may be selected. An instrument ‘fail’ contact is also provided..
Analogue Output
A second analogue output may be specified as a retransmission signal of: process value, set value, deviation or as a control output.
Calibrated Sensor
A UKAS calibrated Pt100 sensor is available for use with the F9000 controller which uses bias features to match the sensor to the controller. Please contact TC Ltd. for details.
Supply
A choice of 85/264V AC or 24V AC/DC supplies is available.